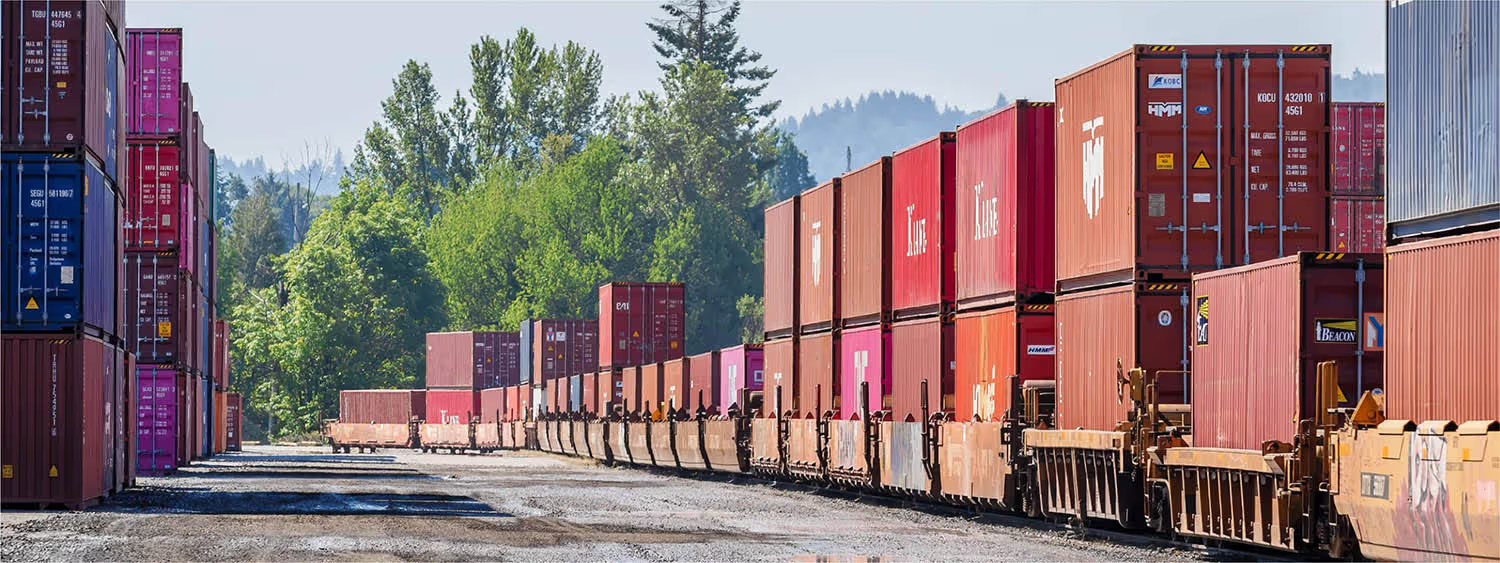
Qualifications
Northwest Container Services boasts extensive qualifications with five strategically located depots in Seattle, Tacoma, Portland, and Boardman, each equipped with a cutting-edge TMS computer system for efficient equipment tracking and inventory management.
.avif)
Overview
In 1986, NWCS joined forces with the Union Pacific Railroad (UPRR) to offer our joint customers an efficient and dependable overnight train service, the "Daily Direct." Since its inception, Daily Direct service has grown from the original three day per week to the current six day weekly schedule between Portland, Tacoma and Seattle terminals.
The success of this unique service is due in part to the close relationship the NWCS team maintains with UPRR personnel, resulting in the best on-time record of any short haul train service in the nation. In support of this on-going partnership with the UPRR, NWCS has continually pledged our commitment to the only rail service of its kind in the Northwest corridor by:
- Establishing an Intermodal Logistics Team dedicated to the Daily Direct service and closely working with UPRR personnel to ensure the consistent on-time schedule our customers have enjoyed for more than 25 years.
- Servicing both domestic and international steamship lines from the NWCS customer base.
- Offering logistical transport of large volumes quickly with one call, fax or e-mail.
In November 2004, NWCS was acquired by Waste Connections (NYSE.WCN) for the purposes of continuing its services for international and domestic marine container transportation services and the addition of transportation of solid wastes to its Finley Buttes landfill in Boardman, Oregon.
Featured Services
NWCS is comprised of five full-featured depots, located in Seattle (2), Tacoma, Portland and Boardman with each offering the following services:
U.S. Customs Bonded Facilities
Our facilities are fenced and secure, capable of handling loads of up to 85,000 pounds. Our staff is trained in working with import and export loads, dealing with steamship and customs releases as they relate to loads. We also offer a chassis pool to assist in the movement of empties and loads should the need arise.
Refrigeration Services
Our facilities have multiple reeferplugs for load storage and monitoring, service pre-trip and repair. NWCS reefer technicians have been trained on all major manufacturers' equipment including: Carrier, Thermo King, Daikin and StarCool.
Hazardous Material Handling
Training in the handling and security of hazardous materials is an ongoing process at NWCS.
Diversified Shops
In addition to typical dry box and chassis repair, we are also able to perform container modifications to customer specifications, or custom-build work on request. Our shops feature multiple enclosed bays to accommodate repairs requiring work to be performed under cover. Parts are quality controlled, and many custom parts can be manufactured on-site as necessary. We also feature "over the road repairs" with our fully equipped service trucks. We are a full service wash-out/steam clean facility.
24/7 Systems Support
Our support systems allow dispatchers to track equipment movement in between the yards, maintain customer inventories, track daily in and out activities, and provide status updates as equipment is repaired and available. Its capabilities include tracking of equipment holds and releases, which can be, broken down by class, type and size. We also offer EDI services to provide our customers real-time updates regarding equipment inventories and movement.
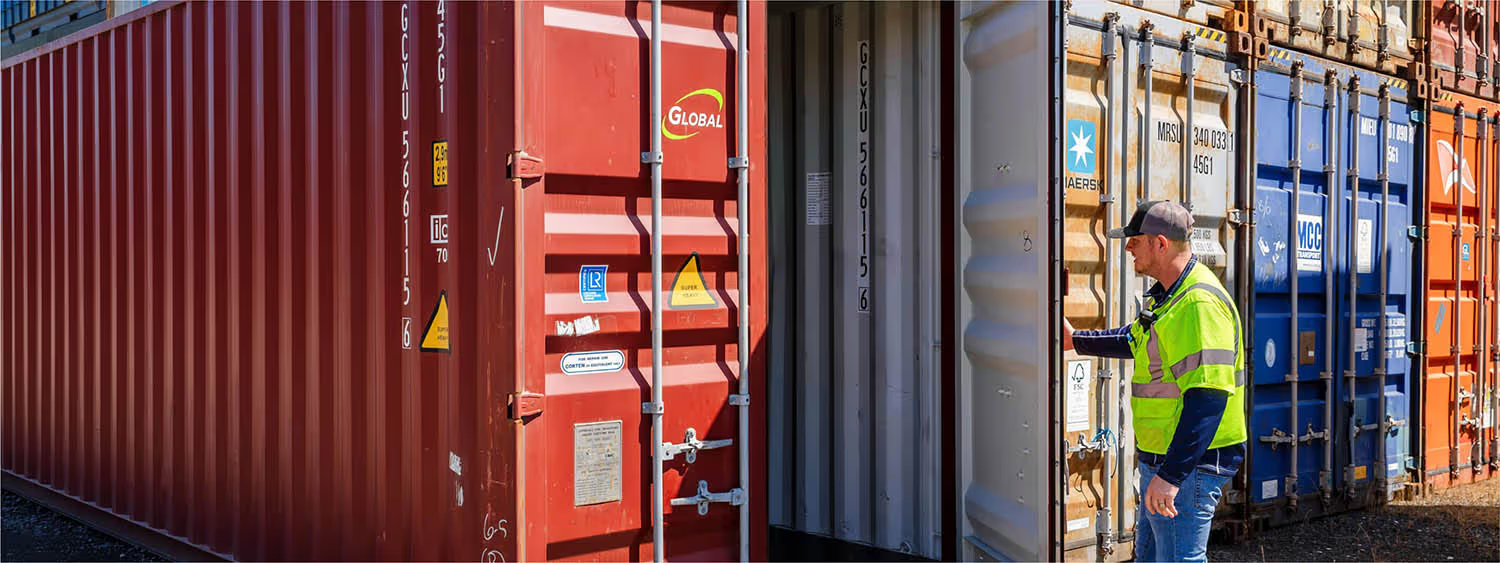
Safety
NWCS has established a goal of leading the industry in environmental health and safety. NWCS has active safety committees at each location that address such issues as worksite safety; environmental/hazardous waste management, and traffic management. To help ensure the safety of our customers, draymen, and employees, NWCS has a very strict drug and alcohol policy including random testing. It is the job of all employees and managers to address the daily issues as they arise when it comes to safety and environmental concerns or incidents.
Accident rates at NWCS have been on a constant decline, but our belief is that all accidents are preventable and that no accident is acceptable.
All major sites that perform maintenance and repair on containers and chassis are equipped with an oil water separator. The oil water separator along with other environmental controls meet or exceed the requirements set by state and federal regulators. These controls help ensure that pollutants do not contaminate the sanitary or storm water systems.
NWCS has also implemented an Accident Prevention Manual for all employees. This manual is a safety guideline for all employees. The manual covers such areas as accident investigation, emergency evacuation, powered industrial truck rules, etc. For example, section 9 of the NWCS Accident Prevention Manual is entitled, "Handling Rail Switches, Derails and Derailments." This section details out the requirements for using derails, switches and intermodal container security. This manual is critical to help ensure the safety of everyone on our site.
Herb Bailey
Safety Coordinator, Western Region
[email protected]
P: 360-207-3861
C: 971-328-2092
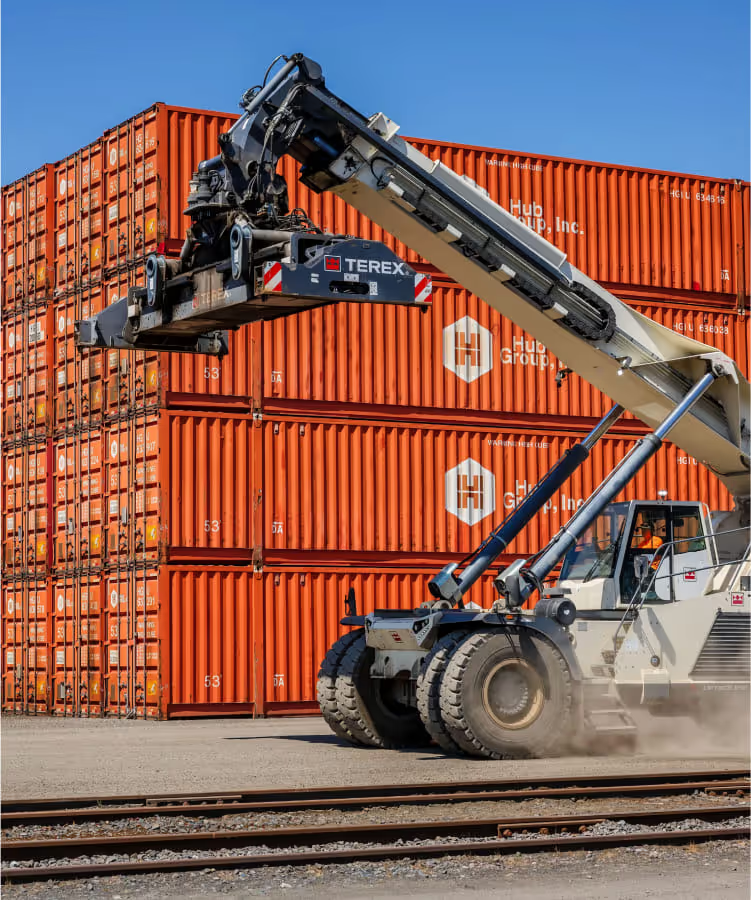
Equipment
NWCS facilities feature state-of-the-art tools and equipment to accommodate all marine container service requests. Our innovative operations team receives continual training, keeping them up-to-date on new equipment and cutting edge techniques.
Equipment List:
- 49ft./5-well rail cars, 115,500 lb capacity, double stack
- 40ft./5-well rail cars, 125,400 lb capacity, double stack
- 48ft/Single well rail cars, 168,500 lb capacity, double stack
- Double rail, 5-high, load container lifts
- Single rail, 5-high, load container lifts
- 10,000 15,000 & 30,000 LB fork lifts
- Gen-sets for intermodal reefer rail logistics
- Yard hostlers
- 20ft, 40ft lease chassis leasing
Managing and maintaining our equipment is of primary importance to NWCS. NWCS mechanics are second to none when it comes to proper preventative and difficult maintenance and repair. Detailed record keeping has provided NWCS with superior equipment utilization.
Craig Kampe
Heavy Equipment Manager
[email protected]
P: 360.990.6983
.avif)
Information Technology
Rob Ainscough
Software Engineer/Manager
[email protected]
P: 503.290.2273
Quinn Davis
Application Developer
[email protected]
P: 971.442.0420
F: 503.468.6518
Honoring our commitments provides our stakeholders peace of mind and establishes us as the premier solid waste services company in the markets we serve. This creates a safe and rewarding environment for our employees while protecting the health and welfare of the communities we serve, thereby increasing value for our shareholders.NWCS continues to be on the leading edge of information technology in our industry. We are committed to implementing the latest information systems for the most accurate data. Our software is designed to link all functions of logistics, container and chassis storage, and maintenance and repair. Communication with our clients is of the utmost importance.
Electronic Data Transfer (EDI)
Capabilities Include: 322, 301, 310, 315, 404, 410 and Westim's